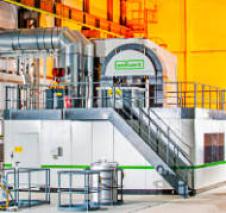
Metal improvement specialist, Wallwork Group, is showcasing new processes designed to extend the service life and improve performance of critical aerospace components. Amidst fuel price increases and challenges to improve environmental performance of aircraft, the company has developed metal treatments that will achieve substantial in-flight fuel savings, sustained performance between scheduled maintenance and extend service life to reduce life-time costs for operators.
Nitron Flight is a family of multi-layer coatings based on titanium, chromium, chromium/aluminium or carbon/metal carbide. Coating systems are applicable to aircraft components including landing gear, engine bearings, engine compressor sections and high temperature engine seals.
The chromium based coating, for example, has been extensively proven with a major international maintenance overhaul and repair contractor on compressor blades. This has been shown to improve fuel consumption by around $48,000 per year, reduce CO2 emissions by around 290 tonnes and maintain the blades optimum aerofoil profile – so that fuel savings are sustained longer and the interval required between overhaul is also further extended.
Nitron O is a titanium based duplex coating ideally suited to improving the surface finish of titanium components to withstand higher loads and remain lubricious. Titanium is increasingly used in aerospace for its high strength to weight ratio and fatigue resistance. However, the coefficient of friction of titanium and the propensity for metal to metal adhesion can undermine these advantages. To overcome these limitations, Nitron O duplex coating, where the titanium surface is first hardened using a plasma based process can be used.
Nitron O duplex coating creates hard and deep nitrided cases in the titanium alloy. Within the same process cycle either a titanium or chromium based layer is then applied by physical vapour deposition (PVD) creating a surface that has steel-like properties making it both lubricious and resilient.
Diamond coating from the Tecvac division of the Wallwork group provides the full spectrum of carbon coatings from highly lubricious graphite films to diamond coating with extreme hardness. Diamond coating is particularly applicable to tools used in the drilling and cutting of aerospace composites. Conventionally hardened tools produce ragged edged cuts causing secondary damage and weakening of the material, while diamond coated tools cut cleanly.
In addition to a full range of traditional vacuum, sealed quench and salt heat treatment processes, Wallwork Heat Treatment have extended their capability into non-ferrous heat treatment with a new aluminium furnace. This will permit the hardening of range of aluminium aerospace components to improve their performance and cost effectiveness.
The Wallwork group has an active programme for technical partnership with aerospace majors and components suppliers. With research and development facilities equal to those found in major universities, the company can refine and develop customised processes and treatment to optimise component performance.
More Information
Simeon Collins, Sales Director, Tel. +44 (0)161 797 9111 Fax. +44 (0)161 763 1861
E-mail: simeon.collins@wallworkht.com Web: www.wallworkht.com
Wallwork Heat Treatment Ltd, Lord Street, Bury, Greater Manchester, BL9 0RE, UK
Press release issued: May 8, 2012
Browse Articles
< Previous |
Next >
Wallwork Group News Archive